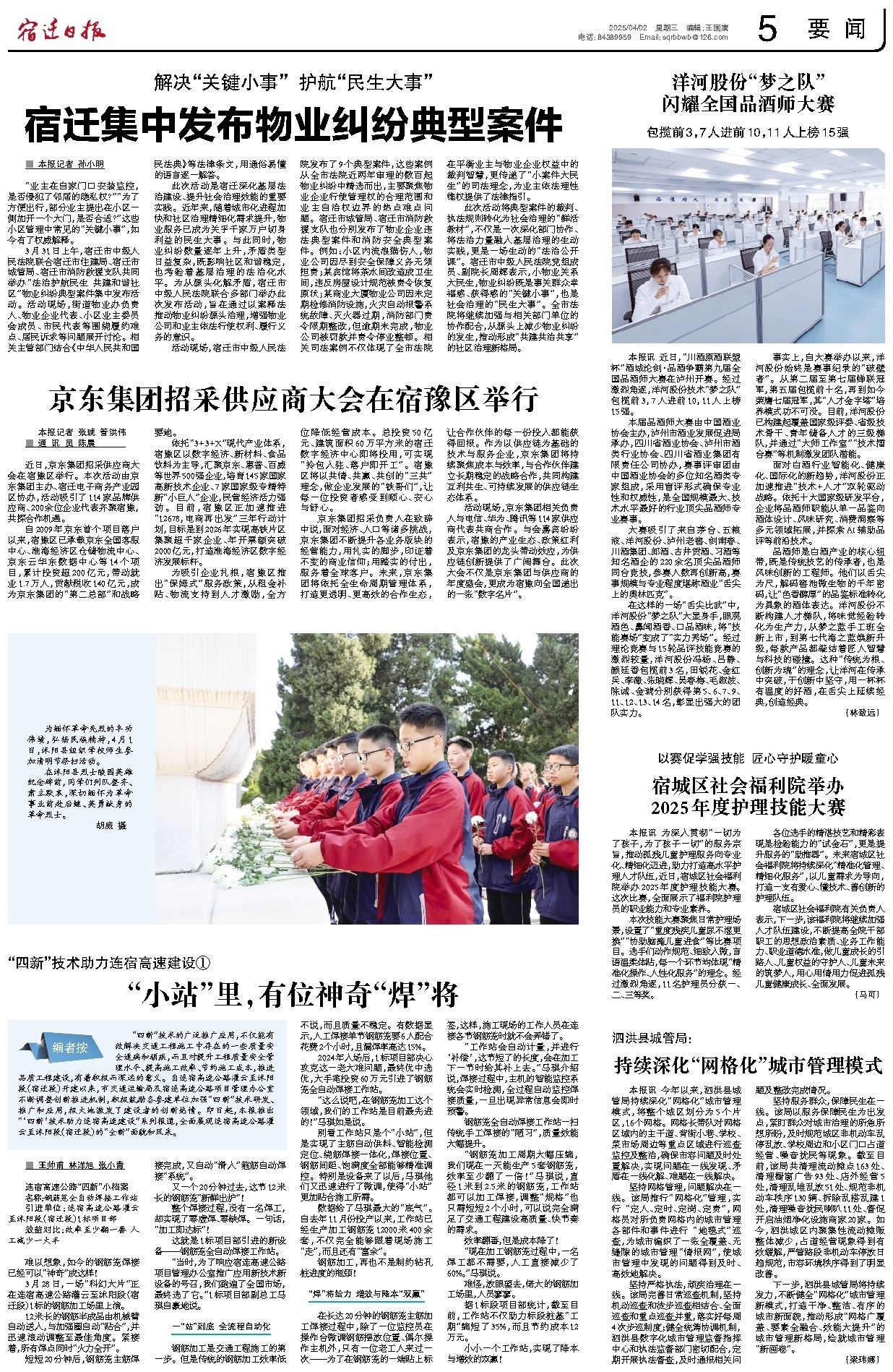
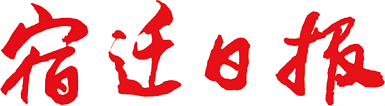
“四新”技术助力连宿高速建设①
“小站”里,有位神奇“焊”将
编者按
“四新”技术的广泛推广应用,不仅能有效解决交通工程施工中存在的一些质量安全通病和顽疾,而且对提升工程质量安全管理水平、提高施工效率、节约施工成本,推进品质工程建设,有着积极而深远的意义。自连宿高速公路灌云至沭阳段(宿迁段)开建以来,市交通运输局及宿连高速公路项目管理办公室不断调整创新推进机制,积极鼓励各参建单位加强“四新”技术研发、推广和应用,极大地激发了建设者的创新热情。即日起,本报推出“‘四新’技术助力连宿高速建设”系列报道,全面展现连宿高速公路灌云至沭阳段(宿迁段)的“全新”面貌和风采。
■ 王帅甫 林洋旭 张小青
连宿高速公路“四新”小档案
名称:钢筋笼全自动焊接工作站
引进单位:连宿高速公路灌云至沭阳段(宿迁段)1标项目部
效益对比:效率至少翻一番 人工减少一大半
难以想象,如今的钢筋笼焊接已经可以“神奇”成这样!
3月28日,一场“科幻大片”正在连宿高速公路灌云至沭阳段(宿迁段)1标的钢筋加工场里上演。
12米长的钢筋半成品由机械臂自动送入,与加强圈自动“贴合”,并迅速滚动调整至最佳角度。紧接着,所有焊点同时“火力全开”。
短短20分钟后,钢筋笼主筋焊接完成,又自动“滑入”箍筋自动焊接“系统”。
又一个20分钟过去,这节12米长的钢筋笼“新鲜出炉”!
整个焊接过程,没有一名焊工,却实现了零虚焊、零缺焊。一句话,“加工即达标”!
这就是1标项目部引进的新设备——钢筋笼全自动焊接工作站。
“当时,为了响应宿连高速公路项目管理办公室推广应用新技术新设备的号召,我们跑遍了全国市场,最终选了它。”1标项目部副总工马琪自豪地说。
一“站”到底 全流程自动化
钢筋加工是交通工程施工的第一步。但是传统的钢筋加工效率低不说,而且质量不稳定。有数据显示,人工焊接单节钢筋笼要6人配合花费2个小时,且漏焊率高达15%。
2024年入场后,1标项目部决心攻克这一老大难问题,最终优中选优,大手笔投资60万元引进了钢筋笼全自动焊接工作站。
“这么说吧,在钢筋笼加工这个领域,我们的工作站是目前最先进的!”马琪如是说。
别看工作站只是个“小站”,但是实现了主筋自动供料、智能检测定位、绕筋焊接一体化,焊接位置、钢筋间距、饱满度全部能够精准调控。特别是设备来了以后,马琪他们又迅速进行了微调,使得“小站”更加贴合施工所需。
数据给了马琪最大的“底气”。自去年11月份投产以来,工作站已经生产加工钢筋笼12000米400余套,不仅完全能够跟着现场施工“走”,而且还有“富余”。
钢筋加工,再也不是制约钻孔桩进度的瓶颈!
“焊”将给力 增效与降本“双赢”
在长达20分钟的钢筋笼主筋加工焊接过程中,除了一位监控员在操作台微调钢筋摆放位置、偶尔操作主机外,只有一位老工人来过一次——为了在钢筋笼的一端贴上标签,这样,施工现场的工作人员在连接各节钢筋笼时就不会弄错了。
“工作站会自动计量,并进行‘补偿’,这节短了的长度,会在加工下一节时给其补上去。”马琪介绍说,焊接过程中,主机的智能监控系统会实时检测,全过程自动监控焊接质量,一旦出现异常信息会即时预警。
钢筋笼全自动焊接工作站一扫传统手工焊接的“陋习”,质量效能大幅提升。
“钢筋笼加工周期大幅压缩,我们现在一天能生产5套钢筋笼,效率至少翻了一倍!”马琪说,直径1米到2.5米的钢筋笼,工作站都可以加工焊接,调整“规格”也只需短短2个小时,可以说完全满足了交通工程建设高质量、快节奏的需求。
效率翻番,但是成本降了!
“现在加工钢筋笼过程中,一名焊工都不需要,人工直接减少了60%。”马琪说。
难怪,放眼望去,偌大的钢筋加工场里,人员寥寥。
据1标段项目部统计,截至目前,工作站不仅助力标段桩基“工期”缩短了35%,而且节约成本12万元。
小小一个工作站,实现了降本与增效的双赢!
江苏路特数字科技有限公司 仅提供技术服务支持, 文字、图片、视频版权归属发布媒体