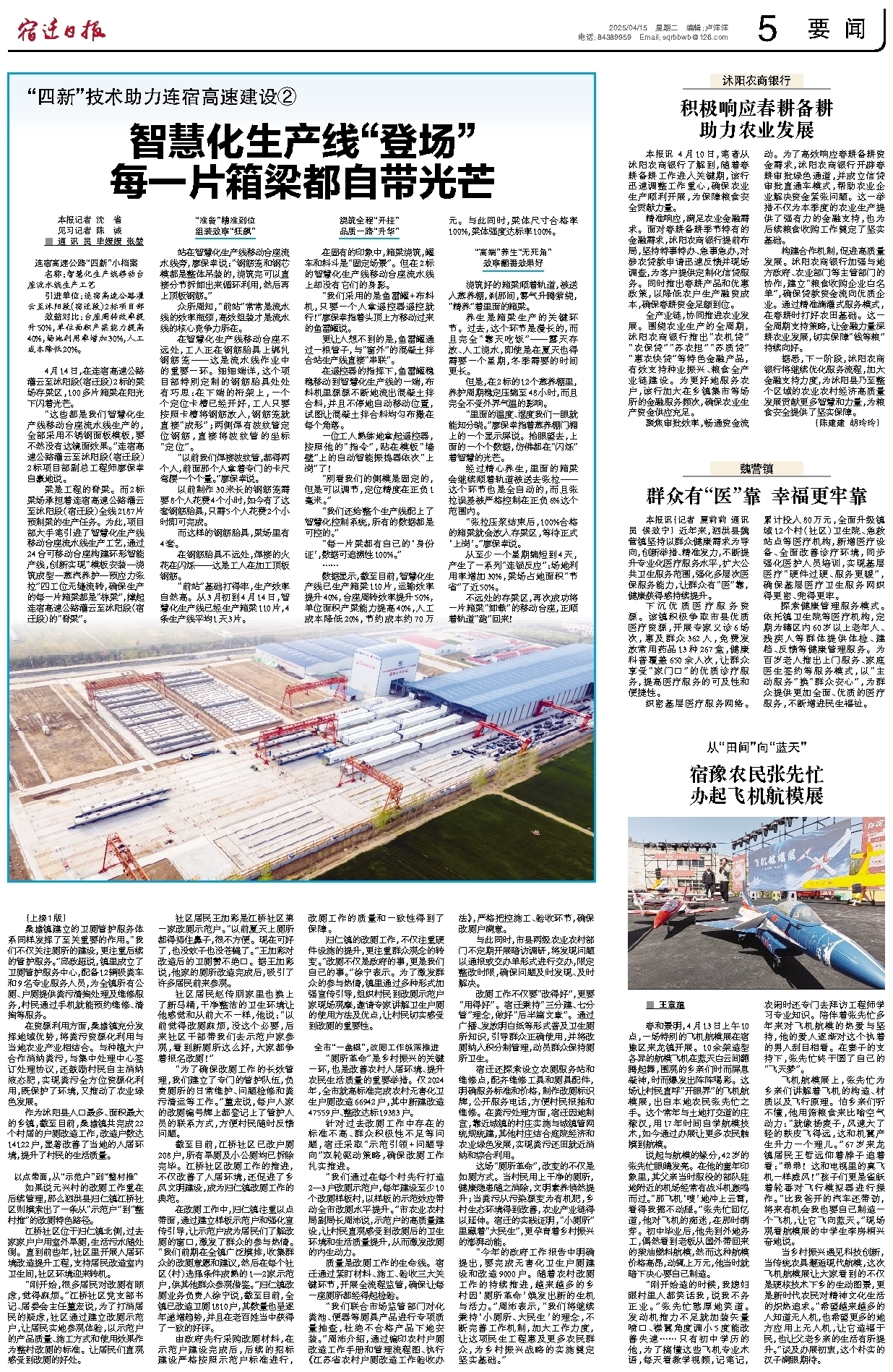
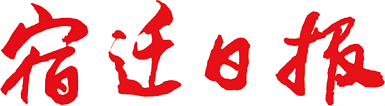
“四新”技术助力连宿高速建设②
智慧化生产线“登场” 每一片箱梁都自带光芒
本报记者 沈 省
见习记者 陈 诚
■ 通 讯 员 毕媛媛 张堃
连宿高速公路“四新”小档案
名称:智慧化生产线移动台座流水线生产工艺
引进单位:连宿高速公路灌云至沭阳段(宿迁段)2标项目部
效益对比:台座周转效率提升50%,单位面积产梁能力提高40%,场地利用率增加30%,人工成本降低20%。
4月14日,在连宿高速公路灌云至沭阳段(宿迁段)2标的梁场存梁区,100多片箱梁在阳光下闪着光芒。
“这些都是我们智慧化生产线移动台座流水线生产的,全部采用不锈钢面板模板,要不然没有这镜面效果。”连宿高速公路灌云至沭阳段(宿迁段)2标项目部副总工程师廖保幸自豪地说。
梁是工程的脊梁。而2标梁场承担着连宿高速公路灌云至沭阳段(宿迁段)全线2187片预制梁的生产任务。为此,项目部大手笔引进了智慧化生产线移动台座流水线生产工艺,通过24台可移动台座构建环形智能产线,创新实现“模板安装—浇筑成型—蒸汽养护—预应力张拉”四工位无缝流转,确保生产的每一片箱梁都是“栋梁”,撑起连宿高速公路灌云至沭阳段(宿迁段)的“脊梁”。
“准备”精准到位
组装效率“狂飙”
站在智慧化生产线移动台座流水线旁,廖保幸说:“钢筋笼和钢芯模都是整体吊装的,浇筑完可以直接分节拆卸出来循环利用,然后再上顶板钢筋。”
众所周知,“前站”常常是流水线的效率瓶颈,高效组装才是流水线的核心竞争力所在。
在智慧化生产线移动台座不远处,工人正在钢筋胎具上绑扎钢筋笼——这是流水线作业中的重要一环。细细端详,这个项目部特别定制的钢筋胎具处处有巧思:在下端的桁架上,一个个定位卡槽已经开好,工人只要按照卡槽将钢筋放入,钢筋笼就直接“成形”;两侧焊有波纹管定位钢筋,直接将波纹管的坐标“定位”。
“以前我们焊接波纹管,都得两个人,前面那个人拿着专门的卡尺弯腰一个个量。”廖保幸说。
以前制作30米长的钢筋笼需要8个人花费4个小时,如今有了这套钢筋胎具,只需5个人花费2个小时即可完成。
而这样的钢筋胎具,梁场里有4套。
在钢筋胎具不远处,焊接的火花在闪烁——这是工人在加工顶板钢筋。
“前站”基础打得牢,生产效率自然高。从3月初到4月14日,智慧化生产线已经生产箱梁110片,4条生产线平均1天3片。
浇筑全程“开挂”
品质一路“升华”
在固有的印象中,箱梁浇筑,罐车和料斗是“固定场景”。但在2标的智慧化生产线移动台座流水线上却没有它们的身影。
“我们采用的是鱼雷罐+布料机,只要一个人拿遥控器遥控就行!”廖保幸指着头顶上方移动过来的鱼雷罐说。
更让人想不到的是,鱼雷罐通过一根管子,与“窗外”的混凝土拌合站生产线直接“串联”。
在遥控器的指挥下,鱼雷罐稳稳移动到智慧化生产线的一端,布料机里源源不断地流出混凝土拌合料,并且不停地自动移动位置,试图让混凝土拌合料均匀布撒在每个角落。
一位工人熟练地拿起遥控器,按照他的“指令”,贴在模板“墙壁”上的自动智能振捣器依次“上岗”了!
“别看我们的侧模是固定的,但是可以调节,定位精度在正负1毫米。”
“我们还给整个生产线配上了智慧化控制系统,所有的数据都是可控的。”
“每一片梁都有自己的‘身份证’,数据可追溯性100%。”
……
数据显示,截至目前,智慧化生产线已生产箱梁110片,运输效率提升40%,台座周转效率提升50%,单位面积产梁能力提高40%,人工成本降低20%,节约成本约70万元。与此同时,梁体尺寸合格率100%,梁体强度达标率100%。
“高端”养生“无死角”
效率翻番效果好
浇筑好的箱梁顺着轨道,被送入蒸养棚,刹那间,雾气升腾萦绕,“精养”着里面的箱梁。
养生是箱梁生产的关键环节。过去,这个环节是漫长的,而且完全“靠天吃饭”——露天存放、人工浇水,即使是在夏天也得需要一个星期,冬季需要的时间更长。
但是,在2标的12个蒸养棚里,养护周期稳定压缩至48小时,而且完全不受外界气温的影响。
“里面的温度、湿度我们一眼就能知分晓。”廖保幸指着蒸养棚门楣上的一个显示屏说。抬眼望去,上面的一个个数据,仿佛都在“闪烁”着智慧的光芒。
经过精心养生,里面的箱梁会继续顺着轨道被送去张拉——这个环节也是全自动的,而且张拉误差被严格控制在正负6%这个范围内。
“张拉压浆结束后,100%合格的箱梁就会放入存梁区,等待正式‘上岗’。”廖保幸说。
从至少一个星期缩短到4天,产生了一系列“连锁反应”:场地利用率增加30%,梁场占地面积“节省”了近50%。
不远处的存梁区,再次成功将一片箱梁“卸载”的移动台座,正顺着轨道“跑”回来!
江苏路特数字科技有限公司 仅提供技术服务支持, 文字、图片、视频版权归属发布媒体